La tecnologia fotovoltaica a perovskite ha fornito efficienze di conversione di energia superiori a qualsiasi film sottile grazie ai processi di deposizione in soluzione e alle peculiari proprietà chimico/fisiche, ma il suo reale sfruttamento a livello di mercato potrà essere fattibile solo se i risultati delle celle di laboratorio (area ˂ 1 cm2) verranno trasferiti a mini-moduli (area ˂ 200 cm2) e sub-moduli (200 cm2 ≤ area ≤ 800 cm2).
Un modulo è composto da un numero di celle collegate in serie per superare la resistenza non trascurabile dei substrati di vetro di ossido conduttivo trasparente (TCO) che induce grandi perdite ohmiche quando la corrente della cella aumenta. Il percorso che porta allo scaling-up dei moduli in perovskite riproducibili, affidabili e ad alta efficienza passa principalmente attraverso l’ottenimento di film di perovskite di alta qualità su larga area e interconnessioni con basse perdite.
La disomogeneità degli strati aumenta quando si realizzano moduli con processi e materiali ottimizzati per celle di piccola area. A causa della natura policristallina del film di perovskite, possono verificarsi difetti ai bordi dei grani e vacanze durante il processo di fabbricazione. Quando si scala fino alle dimensioni del sub-modulo, le perdite dovute alla disomogeneità degli strati hanno un enorme impatto sulle prestazioni del dispositivo e sono principalmente legate alla tecnica di deposizione, alla composizione del materiale e all’ambiente di deposizione. Oltre agli sforzi sui mini-moduli, lo sviluppo di processi di produzione su larga scala per i sub-moduli è fondamentale per fornire una transizione rapida ed economica verso la produzione di massa di pannelli in perovskite.
Nonostante i grandi sforzi compiuti in letteratura per scalare la tecnologia fotovoltaica in perovskite, pochi lavori hanno affrontato la fabbricazione di sub-moduli per diversi motivi. Innanzitutto, la tecnica di spin-coating, ancora ampiamente utilizzata per la fabbricazione di mini-moduli, non può essere considerata un metodo di deposizione scalabile e richiede solitamente un’intensa pratica manuale per produrre una deposizione uniforme senza difetti. Inoltre, i processi realizzati in azoto con l’ausilio di una glove-box, sono costosi rispetto a quelli realizzati in aria ambiente e non replicabili in un impianto reale. Infine, il processo di produzione dovrebbe soddisfare alcuni requisiti fondamentali: sostenibilità ambientale, basso costo, produzione affidabile e ad alto rendimento, buone prestazioni e stabilità del dispositivo.
In un recente lavoro pubblicato sulla rivista Progress in Photovoltaics: Research and Applications, Il CHOSE (Centre for Hybrid and Organic Solar Energy), Dipartimento di Ingegneria Elettronica dell’Università degli Studi di Roma Tor “Vergata”, il Dipartimento di Biotecnologia, Chimica e Farmacia (R2ES Lab) dell’Università di Siena, il CNR-ICCOM (Istituto per la Chimica e i Composti Metallo Organici) e il CNR-ISM (Istituto di Struttura della Materia), mostrano lo scaling-up della tecnologia fotovoltaica a perovskite fino alle dimensioni del sub-modulo (320 cm2 di area totale, 201 cm2 di area di apertura, 186.1 cm2 di area attiva) mediante un processo di deposizione “hybrid meniscus coating” (blade-coating e slot-die coating) in aria ambiente fuori dalla glove-box (Figura 1).
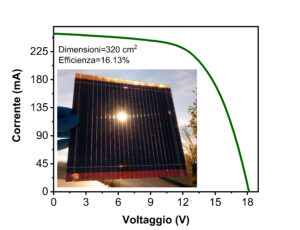
Immagine: CHOSE
Oltre al beneficio derivante dall’ottimizzazione dei processi di deposizione, la passivazione della perovskite e l’utilizzo di un solvente con un’elevata pressione vapore hanno permesso di sopprimere rispettivamente le perdite di ricombinazione non radiativa e controllare la formazione dei nuclei. Questa è stata la prima volta che un sub-modulo è stato fabbricato al di fuori della glove-box mediante tecniche di deposizione scalabili e a basso costo. L’omogeneità dimostrata dell’intero stack ha consentito di raggiungere un’efficienza record del 16.13% con un 93% di area utile occupata (Figura 2). Le perdite rispetto ad una cella di piccola area sono state solo del 7% e le prestazioni sono uguali a quelle di un mini-modulo realizzato con tecnica di deposizione blade-coating. Il sub-modulo fabbricato è rimasto stabile al test ISOS-D-1 per più di 3000 ore.
I presenti contenuti sono tutelati da diritti d’autore e non possono essere riutilizzati. Se desideri collaborare con noi e riutilizzare alcuni dei nostri contenuti, contatta: editors@nullpv-magazine.com.
Inviando questo modulo consenti a pv magazine di usare i tuoi dati allo scopo di pubblicare il tuo commento.
I tuoi dati personali saranno comunicati o altrimenti trasmessi a terzi al fine di filtrare gli spam o se ciò è necessario per la manutenzione tecnica del sito. Qualsiasi altro trasferimento a terzi non avrà luogo a meno che non sia giustificato sulla base delle norme di protezione dei dati vigenti o se pv magazine ha l’obbligo legale di effettuarlo.
Hai la possibilità di revocare questo consenso in qualsiasi momento con effetto futuro, nel qual caso i tuoi dati personali saranno cancellati immediatamente. Altrimenti, i tuoi dati saranno cancellati quando pv magazine ha elaborato la tua richiesta o se lo scopo della conservazione dei dati è stato raggiunto.
Ulteriori informazioni sulla privacy dei dati personali sono disponibili nella nostra Politica di protezione dei dati personali.